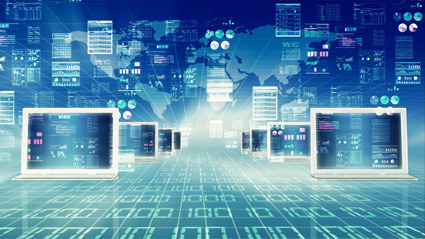
「設備稼働率」「生産効率」を高めるためには、最適な生産計画と投入順序の立案が必要不可欠ですが、最新の手法として「仮想工場(バーチャルファクトリー)」の活用が注目を集めています。仮想工場をPC上に作り、生産シミュレーションにより、最適解を導き出す手法です。「テジタルツイン」「サイバーフィジカルシステム(CPS)」という表現をする場合もあります。
では、生産計画立案で良く使われる「生産スケジューラ」と、「生産シミュレーション」はどのように違うのでしょうか?
1. 生産スケジューラとの違い
市販の生産スケジューラは多くありますが、その殆どはガントチャートを用いて、製造するワークの工程順に、該当する設備を手動で割当てて、生産順序を策定します。そのため、「受注済みオーダーの完成予定時期の予測」「設備や作業者の負荷状態の予測」といった“予測”に対しての活用や、パラメータを調整することで「製造日程計画」「作業指示計画」などを含めた「生産計画」の策定、検証をする際に有益なツールです。
一方、生産シミュレーションを用いて最適生産計画を策定する場合、生産ラインのモデルをコンピューター上に作り、当該モデルにワークを投入して、最適な計画順序を探します。上述の“予測”はもちろん、製造日程計画の作業指示も、各設備能力や段取り時間も含めてパラメータとして入力することで、最適な製品投入順序を自動で導く事もできます。生産スケジューラに比べて、より詳細に設備側のパラメータを調整でき、最適値を自動で導いてくれる点が大きな違いです。
2. 生産シミュレーションを用いた「最適生産計画」立案のメリット
生産シミュレーションを活用することで、無数に近い計画順序から、制約条件を満たし、かつ目標とする数値が最も良い順序を探し出すことができます。ここで、全ての計画順序を探してシミュレーションする方法はバックトラッキングと言われていますが、非常に計算量が多くなり、結果としてPCの負荷が重くなり、結果が出るまでに時間がかかります。
これに対して現在は、効率良く最適解を見つけるアルゴリズムが数多く研究され、実用化されています。その一つに遺伝的アルゴリズム(GA : Genetic Algorithm)があります。全てを探索すると50種類のワークであっても50!(50×49×・・・)=約3×10^64に及ぶ天文学的な数字となってしまいます。そのためいくらパソコンが進化しても計算効率の良い探索方法は有効な手法です。
このような探索方法を有した生産シミュレーションを用いた最適生産計画を行う主なメリットは以下になります。
(1) あらゆる条件を加えることができる
例えば、納期遵守はもちろん、特定の工程での着手日時の遵守など時間的な制約を加えることが可能です。また、特定のバッファへの投入制限など物理的な条件を加味することもできます。
(2) あらゆる目的関数で評価することができる
例えば、生産スケジューラを用いた場合、通常はガントチャートを見ながら、各設備の稼働率を高められる様にムダのない計画を立てます。一方で、生産シミュレーションを用いる最適生産計画では、設備の稼働率を最大化できる条件だけでなく、リードタイムの短縮、バッファ容量(中間在庫)最適化など、指定した制約条件下で、設定した指標に最も合致した計画順序を得ることができます。
(3) シミュレーションで評価ができる
最適な計画順序でシミュレーションをすることによるメリットは他にもあります。例えば、投入したワークのリードタイム、各設備の稼働率、各バッファの滞留率、作業者をモデルに取り入れることで、各作業者の稼働率のデータを得ることができます。これらの細かなデータを得ることができるのは生産シミュレーションの真骨頂でもあります。
ガントチャートによる計画の出力もできます。そのため、各工程で各ワークの投入時間、排出時間もログとして得られます。このようなログデータは各工程の外段取りを進める上で非常に有益なデータとなります。
パソコン上のバーチャルファクトリーで何度も繰り返してシミュレーションを行って最適な生産計画順序を算出するため、市販の生産スケジューラを上回る機能があると思われがちですが、課題も当然あります。
(1) 細かな生産計画の調整がしにくい
ガントチャート上で、全体の稼働状況を見ながら生産計画を変更することはできません。
(2) BOM(Bill Of Materials:部品表)からの部品情報を展開ができない
関連部品の在庫引き当て、又部品の発注タイミングまでの機能はありません。
上記機能も含めて生産計画を立案したいのであれば、市販のスケジューラと併用して行うのがベストと考えます。
4. 生産シミュレーションを用いて最適生産計画を立案するのに必要なデータ
生産シミュレーションを実行する際に必要な主なデータは以下になります。
(1) 生産計画データ
投入予定のワークのデータ
(2) 工程関連データ
各工程でのワークの処理数、バッファ容量
(3) 工順データ
投入予定のワークの工順
(4) 処理時間、段取時間データ
投入予定のワークが各工程で処理される時間及び段取時間
関連データはExcelデータ(表2,3)に記入します。
5. バーチャルファクトリーモデル
先のデータを弊社が用意したバーチャルファクトリーモデルに入力することで、自動的にモデル(図2)が生成され、シミュレーションが自動実行されます。図のモデルの各工程は設備及びバッファから成り立ち、各工程の仕様はExcelファイルから付与されます。
6. 出力結果
何度もシミュレーションを繰り返した後、最適な生産計画(理論的には限りなく最適に近い“近似解”)が出力されます。それだけではなく、各工程の稼働率、各ワークのリードタイム及び各工程でのワークの投入時間と排出時間の履歴も出力されます。
7. まとめ
日々の生産計画立案は、大変重要な業務です。一方で、納期等の制約条件を遵守して、生産スループットを最大限高めることはとても難しく、時間も掛かります。これを「生産シミュレーション」の技術を活用し、パソコンで最適解をだすことで、計り知れない恩恵が得られます。また、搬送時間、工程の設備故障率などを入力することで、生産ラインの能力評価もできます。
特にジョブショップ型の生産方式において、多品種少量で段取り回数が生産性に大きく関与している場合に、この「生産シミュレーション」から導かれた各種最適解は、大きな効果をもたらします。